首页 丨 集团介绍丨 主营业务 丨 主要业绩丨 党建工作丨 新闻中心丨 职工之家丨 招贤纳士丨 联系我们丨 网站地图丨 集团邮箱
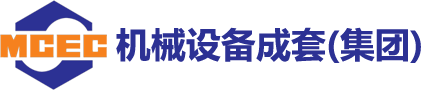
浅谈设备产品的质量控制 集团工程公司 朱锦明/文 一、产品的设主控制 设备产品设计控制包括设计输入、设计输出及设计评审、设计验证、设计确认和设计更改控制。 1.设计输入控制。 它是以产品标准为基础形成的文件,设计输入是产品满足顾客、法律、法规要求的根据,所以设计输入应子评审,并有书面记录。 2.设计输出及设计评审控制。 设计输出就是产品的设计图样,对设计输出应进行评审。评审其与标准的符合性,技术的先进性以及经济性、工艺性、标隹化等。评审应有书面记录。设计输出应经批准后才能发布。 3.设计验证控制。 在产品形成的适当阶段实施验证,证明与设计输入的符合性。 4.设计确认控制。 设计确认以验证记录和实施运行,证明产品满足预期的要求。 5.设计更改控制。 不论是来自外部的或内部的更改要求,都应进行评审和授权人批准,方可实施更改。 6.送国家授权检验机构作审查。 二、原材料的质量控制 1.供应厂商的选定由技术、工程、采购、质检部门负责对供应厂商的考查、评估、确认、定点。 2.供应厂商必须具备有质量保证体系、供货能力、投诉处理及服务能力,才能列入被评估供应厂商。 3.通过评估资格的供应厂商采用送样、少量试用、小批量试用、中批量试用全部合格,并具备以上条件的供应厂商才能列入采购定点单位。 4.原材料进厂必须由质检部严格按采购清单,及原材料检验技术标准进行验收并记录方可入库,杜绝不合格的原材料入库,流入生产线。 5.原材料做到合理、正确摆放,标示明确。遵守先进先出的原则,防止库存时间过长而变质。 6.保证仓库通风良好,并随时监测仓库的温度、湿度等控制在允许范围内。 三、外购设备的选型与购置 外购设备选型是指通过技术经济分析,从能满足需要的多种型号设备中选购最佳者的决策。合理地选择设备,可使有限的资金发挥最大的经济效益。 1.设备选型应遵循的原则是:经济合理,技术先进,生产适用,三者应统一权衡。 2.设备选型应考虑的问题主要有:质量、价格、交货期、技术经济效果、可靠性和维修性、节能、以及制造厂家的信用和售后服务。 3.采购方应组织对供货单位的质量管理评审,全程监控加工设备产品质量。 四、生产过程的质量控制 1.加工工艺文件控制。 凡工艺的正确与否影响产品质量的,都应制定相应的作业指导书。作业人员应能方便地获得这些文件。 2.人员控制。 凡是特殊工艺须专门人员操作的,应对操作人员进行培训,经考试合格,方能上岗操作。 3.设备工装控制。 设备控制的要点是合理使用,精心保养,定期检查,即时维修,必要时还须调整和测定机械能力,使机械能力能够符合工序质量的要求。 4.工作质量的控制。 工作质量的好坏,是保证产品质量的关键所在。 5.工艺过程控制。 工艺过程控制包括:配备符合要求的加工设备;配备必要的检验人员和检验设备;严格工艺纪律,制止不按工艺文件的操作;严格工序下转之间的检验并记录;不合格件不得转序,并严格隔离。 6.见证点和停止点的质量控制。 质量控制点在设备采购合同中体现,并在生产厂家质量计划中细化,根据设备生产进度节点,生产厂家以书面方式通知采购方,参加见证点和停止点的质量活动。 五、质量检验控制。 1.工序检验控制。 严格每道生产工序的工序检验,并作记录、标识,必要时可以追溯。 2.成品检验控制。 开发的产品应作型式检验。型式试验合格的产品,在型式试验有效期内,无特殊情况时,只做出厂检验。 3.出厂检验控制。 出厂检验必须在过程检验后进行。出厂检验合格者方可记账、入库。检验不合格者应隔离,等待处理。让步接受时,应有顾客签字并通知相关方。 六、成品仓库的质量控制 1.成品仓库保证通风良好,温、湿度控制在允许范围内。 2.产品堆放整齐。仓库产品严格按先进先出的原则,杜绝存放时间过长,影响产品质量。 3.产品包装必须符合运输要求。 |
浅谈设备产品的质量控制 集团工程公司 朱锦明/文 一、产品的设主控制 设备产品设计控制包括设计输入、设计输出及设计评审、设计验证、设计确认和设计更改控制。 1.设计输入控制。 它是以产品标准为基础形成的文件,设计输入是产品满足顾客、法律、法规要求的根据,所以设计输入应子评审,并有书面记录。 2.设计输出及设计评审控制。 设计输出就是产品的设计图样,对设计输出应进行评审。评审其与标准的符合性,技术的先进性以及经济性、工艺性、标隹化等。评审应有书面记录。设计输出应经批准后才能发布。 3.设计验证控制。 在产品形成的适当阶段实施验证,证明与设计输入的符合性。 4.设计确认控制。 设计确认以验证记录和实施运行,证明产品满足预期的要求。 5.设计更改控制。 不论是来自外部的或内部的更改要求,都应进行评审和授权人批准,方可实施更改。 6.送国家授权检验机构作审查。 二、原材料的质量控制 1.供应厂商的选定由技术、工程、采购、质检部门负责对供应厂商的考查、评估、确认、定点。 2.供应厂商必须具备有质量保证体系、供货能力、投诉处理及服务能力,才能列入被评估供应厂商。 3.通过评估资格的供应厂商采用送样、少量试用、小批量试用、中批量试用全部合格,并具备以上条件的供应厂商才能列入采购定点单位。 4.原材料进厂必须由质检部严格按采购清单,及原材料检验技术标准进行验收并记录方可入库,杜绝不合格的原材料入库,流入生产线。 5.原材料做到合理、正确摆放,标示明确。遵守先进先出的原则,防止库存时间过长而变质。 6.保证仓库通风良好,并随时监测仓库的温度、湿度等控制在允许范围内。 三、外购设备的选型与购置 外购设备选型是指通过技术经济分析,从能满足需要的多种型号设备中选购最佳者的决策。合理地选择设备,可使有限的资金发挥最大的经济效益。 1.设备选型应遵循的原则是:经济合理,技术先进,生产适用,三者应统一权衡。 2.设备选型应考虑的问题主要有:质量、价格、交货期、技术经济效果、可靠性和维修性、节能、以及制造厂家的信用和售后服务。 3.采购方应组织对供货单位的质量管理评审,全程监控加工设备产品质量。 四、生产过程的质量控制 1.加工工艺文件控制。 凡工艺的正确与否影响产品质量的,都应制定相应的作业指导书。作业人员应能方便地获得这些文件。 2.人员控制。 凡是特殊工艺须专门人员操作的,应对操作人员进行培训,经考试合格,方能上岗操作。 3.设备工装控制。 设备控制的要点是合理使用,精心保养,定期检查,即时维修,必要时还须调整和测定机械能力,使机械能力能够符合工序质量的要求。 4.工作质量的控制。 工作质量的好坏,是保证产品质量的关键所在。 5.工艺过程控制。 工艺过程控制包括:配备符合要求的加工设备;配备必要的检验人员和检验设备;严格工艺纪律,制止不按工艺文件的操作;严格工序下转之间的检验并记录;不合格件不得转序,并严格隔离。 6.见证点和停止点的质量控制。 质量控制点在设备采购合同中体现,并在生产厂家质量计划中细化,根据设备生产进度节点,生产厂家以书面方式通知采购方,参加见证点和停止点的质量活动。 五、质量检验控制。 1.工序检验控制。 严格每道生产工序的工序检验,并作记录、标识,必要时可以追溯。 2.成品检验控制。 开发的产品应作型式检验。型式试验合格的产品,在型式试验有效期内,无特殊情况时,只做出厂检验。 3.出厂检验控制。 出厂检验必须在过程检验后进行。出厂检验合格者方可记账、入库。检验不合格者应隔离,等待处理。让步接受时,应有顾客签字并通知相关方。 六、成品仓库的质量控制 1.成品仓库保证通风良好,温、湿度控制在允许范围内。 2.产品堆放整齐。仓库产品严格按先进先出的原则,杜绝存放时间过长,影响产品质量。 3.产品包装必须符合运输要求。 |